![[Translate to Englisch:] Pfistermühle](/fileadmin/_processed_/0/4/csm_Pfistermuehle_Titel_bff973e428.jpg)
The historic Pfistermühle in the heart of Munich
The Pfistermühle is located in the heart of the old town of Munich and is part of the Platzl Hotel building complex. The Pfistermühle was originally built in 1578/79. In the course of time, significant changes were made to the building. Unfortunately, the building was severely damaged by a bomb during the Second World War, so that only parts of the ground floor and parts of the outer walls have been preserved.
In the 1980s, the current part of the Pfistermühle building was rebuilt. The building stands out not only because of its excellent location, but also because of its historic façade with striking vine growth, making it an eye-catcher with a high recognition value. Like the Platzl Hotel, the Pfistermühle is operated by Platzl Hotel Inselkammer KG. The Pfistermühle is connected to the hotel complex via a connecting building.
Currently, the ground floor of the Pfistermühle is home to a restaurant, which will remain there in the future. On the first floor you will find meeting rooms, while floors two to four are used as staff rooms. The attic floor (fifth floor) provides space for the ventilation systems of the entire building.
Soon, storeys two to five will be converted into 13 high-quality hotel suites, which will then offer exclusive overnight accommodations in the center of Munich. The conversion is complex and requires both the redesign of walls and ceilings and the construction of a new staircase. The building shell, the restaurant business and the conference rooms will be retained, and these will continue to operate at the same time during the construction phase.
The accommodation of the new ventilation technology poses a particular challenge: In the existing building, all ventilation systems are located on the fifth floor, in the control center in the attic. Since the bedrooms of the two-storey suites will be built here, the new ventilation units will have to be relocated to technical control centers to be built.
For this purpose corresponding rooms will be created in the intermediate building between Pfistermühle and Platzl Hotel. The ventilation systems of the kitchens, the guest room and the conference rooms are also to be integrated into the new concept.
The MEP design
A lot of technology in a small space
Restaurant, kitchen, hotel rooms, conference rooms - technical solutions had to be developed for all these different use cases. The particular challenges here were the confined space and the historic building structure, which had already been altered several times.
Creation of the 3D architecture model
Before the MEP design could begin, the architecture had to be modeled. This was done by Volanteq itself since no 3D model had been created by the architect. The basis for this was again the results of the building measurement and the 2D plans provided by the architect.
In this context, it quickly became apparent that the building had a wide variety of wall thicknesses and courses. The possibility of using LINEAR’s solutions to measure the wall thicknesses in the model and to model walls of the same thickness proved to be extremely useful here.
The storey table also made it possible to arrange the different storey heights of the main building and the two ancillary buildings simply and clearly. It was thus possible to generate a model of the existing building within a short time using LINEAR’s solutions on Autodesk Revit. This was not only a necessary and important tool for coordinating the different disciplines in a very confined space, but also served to perform the necessary calculations.
Model-based load calculations
The self-created 3D architectural model formed the basis for the following load calculations and made it possible to calculate both the heat and cooling load directly from the information in the model. For this purpose, MEP spaces had been created based on the architectural model and provided with room information, such as usage, number of persons and target values. With the help of this information, the heat and cooling loads as well as the minimum outdoor air volume flows could then be calculated directly. The smooth exchange of information between the model and the calculation modules ensured fast and error-free implementation.
Design of the technical systems
The results of the load calculations were used to design the technical systems. As is often the case, the limited space available for the technical equipment presented the biggest challenge. In order to occupy as little space as possible in the prestigious main building, the technical equipments were placed in annexes and attic rooms, where they are as well hidden from the eyes of hotel guests.
Due to the different uses, however, a total of four separate ventilation systems had to be located. In addition, there were technical rooms for the heating and cooling systems, including their respective distribution. Meanwhile, the two technical rooms are supplied via the main control centers in another part of the building complex, which are connected to the district heating and cooling network. Here, too, Volanteq provided a convincing concept for the realization of the connections to the network.
Individual temperature control for the hotel rooms
All hotel rooms are heated and cooled by means of fan coils, which are connected via a four-pipe system and have a primary air connection, which in turn is supplied by one of the air handling units in order to guarantee the minimum outdoor air volume flow. In addition, underfloor heating is used in the rooms, and heating/cooling ceilings are used for basic temperature control on the upper storeys. The underfloor heating, the fan coils and the air handling units are supplied via three separate heating networks and two separate cooling networks, so that they meet the different temperature requirements of the consumers and allow individual control for each hotel room.
New potable water and waste water system
The potable water and waste water system for the future hotel use presented a special challenge because the building was not originally designed for use as a hotel. To solve this, cooperation with a manufacturer was established at an early stage and their products were integrated into the design via the LINEAR CAD library.
From network calculations to tender
All calculations for the networks could be carried out with LINEAR, from dimensioning to pump and valve layout to selecting the right insulation thickness. The numerous visualization options made it possible to illustrate all calculation results and quickly identify any anomalies.
In this way, the detailed and realistic implementation not only creates added value in the design, but additionally provides a usable model for the building owner, which brings long-term benefits.
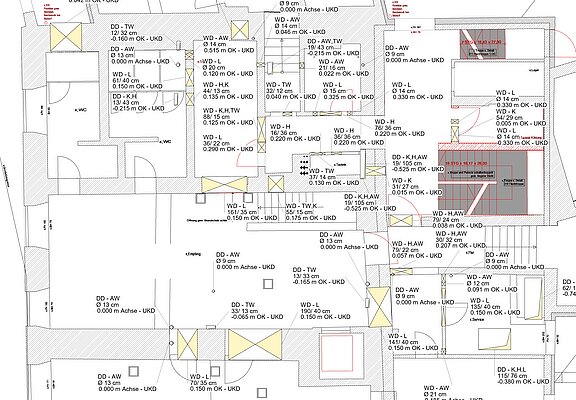
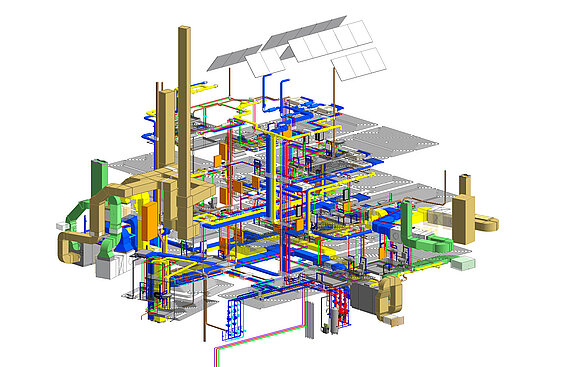
Collaboration with the structural engineer
After successful calculation of all installations, coordination with the structural engineer took place, where comprehensive measures were also required to make hotel operation possible. The preparation of the void planning could then be smoothly coordinated and executed with the other parties involved with the help of the LINEAR Void Manager.
Detailed design for the construction and utilization phase
One of the last steps is the construction design, which is simplified by the straightforward selection of disciplines in the LINEAR Control Board and the associated view filters. In the end, the model has a very high quality and allows for further usage during construction and building operation to ensure an efficient and successful implementation of the project.
During the construction period, a viewer is made available to the executing companies, which is not only used for pure visualization, but also serves as a tool for construction management. In this way, design and execution can be reconciled on site: Spots requiring coordination can be marked in the model and linked together with a photo of the actual situation to create tasks and assign them to employees. The goal is to have an advanced model at the end of the construction period that represents the as-built status and is linked to information on maintenance and operation of the components. This allows the owner and operator to easily get a quick overview of their building and systems.
In this way, the detailed and realistic implementation not only creates added value in the design, but additionally provides a usable model for the building owner, which brings long-term benefits.
BIM by conviction
The fact that existing buildings are subject to change over time, both in terms of technical systems and types of use, requires a fundamental rethinking of building technology in every project. In the process, one often finds that the existing documentation is deficient or incomplete, as it is usually available as a DWG, PDF or even in paper form. Often, this documentation is not consistently updated, which leads to the fact that important information about the facilities is only available to those who are familiar with the object, such as FM service providers, maintenance companies and building technicians. This inevitably leads to information being lost over time.
To counteract this problem, Volanteq has developed an approach in which the existing floor plans are arranged on top of each other at least in three-dimensional space in accordance with the height or, depending on the customer’s requirements, a BIM-capable building model is created in which the existing system technology has then been replicated. The resulting digital twin is initially only a means to an end, because the main advantage of this method is that the relevant data can be clearly assigned to the graphical components in the model. On this basis, holistic calculations can then also be carried out and subsequent changes and information can be entered directly into the model. The possibility of linking the database with a higher-level database management system, for example, in order to generate mass extracts of currently available components for maintenance tenders and to process the object-related maintenance documentation, is a trend-setting feature.
Finally, this enables the MEP designers, contractors and FM service providers involved to update the documentation in a consistent, sustainable, and technically correct manner.
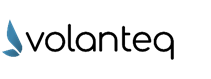
Volanteq GmbH, based in Munich, is an innovative design office that specialized in the optimization of existing buildings and their systems engineering in commercial buildings and medium-sized businesses already years ago. The team of engineers develops demand-oriented and interdisciplinary, co-ordinated technology concepts for all building services.
Volanteq GmbH
Hofmannstrasse 7a
81379 München