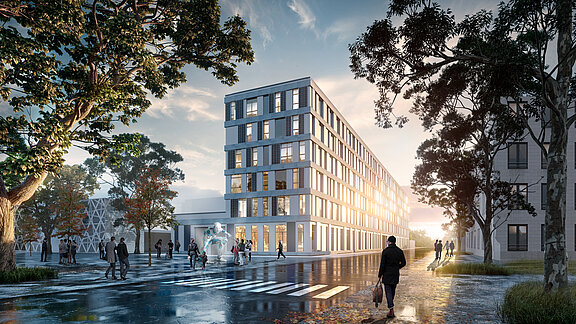
Fig. 1: © Brückner Architekten München
Since its foundation in 1983, the company’s headquarters have been located on a 24,000 m² site on Westendstrasse in Munich. As part of the “Algorithm Headquarters TÜV SÜD” project designed and implemented by the architecture firm Brückner Architekten München, the existing old buildings at the rear of the site were demolished and replaced by a modern, sustainable building unit that offers around 600 modern workplaces. The main goal of the new building is to create attractive and modern working conditions for employees while at the same time significantly reducing energy consumption. TÜV SÜD is relying on Building Information Modeling (BIM) for this project and is relying on the longstanding expertise of LINEAR customer PLANplus in the area of MEP design.
Sustainability as a guiding principle
During the design phase, particular emphasis was placed on sustainable construction and management. A comprehensive analysis of solar radiation and its intensity formed the basis for optimizing the façade and interior design. The building is largely cooled and heated using its own groundwater well and district heating from the public utility company of Munich. This ensures a virtually emission-free energy supply. The building meets the highest efficiency standards and is certified in accordance with the “DGNB Gold” sustainability standard.
Consistent BIM by PLANplus
PLANplus has been committed to consistently handling all new projects as BIM projects since 2015. This includes design and implementation planning, coordination and data transfer to contractors for the construction planning. In this project, heating, ventilation, cooling, plumbing, measuring and control as well as sprinklers were implemented. From the outset, project handling was based on a model that was developed using cloud-based digital collaboration. The prerequisite for integratd design was the BIM processing of the commissioned architecture firm, which provided a quality basic model for further processing. The scope of the commissioned technical building equipment (HVAC/MEP/I&C/SPR) is estimated at EUR 15,000,000 and includes the design and execution of the systems for:
Heating
- Heat load calculation
- Pipe network calculation
- Heating dimensioning
Sanitary
- Potable water network
- Hot water
- Siphonic systems
- Gas distribution network
Climate Control
- Cooling load calculation
- Energy demand calculation
Ventilation
- Ventilation network
- Air and volume flow calculation
- Pressure loss/balancing
- Air duct dimensioning
- Domestic ventilation
Electrical Installations and Building Automation
- Power supply
- Lighting
- Communication and security technology
Transportation technology
Dynamic BIM execution plan as the Basis
The data exchange between the specialist MEP designer and other project participants was precisely organized via a dynamic BIM execution plan. BIM-compliant design ensured a consistent flow of information from early design stage to the construction design. Data was exchanged using the IFC format. The Revit format was used for construction design, as the contractor also worked with Revit. This significantly simplified cloud-based collaboration.
The calculation and simulation programs used by the project participants therefore had to be able to exchange data with other software solutions used in the project through bidirectional, standardized interfaces (e.g. IFC). This reduced the effort required to enter master data and made it easier to update the calculation models when changes were made to the 3D model. LINEAR solutions were used for the calculations and simulations required for the HVAC and MEP systems. This way it was possible to work directly on the central data model.
In this project, the BIM execution plan was the key document during the course of the BIM and MEP design and was created through collaboration between the specialists under the leadership of the BIM manager. This is where those involved can find answers to most questions relating to digital project management. The BIM execution plan was constantly scrutinized over the course of the project and adapted as conditions changed. In this way, the cooperation of those involved was optimized in a continuous improvement process over the course of the project.
Detailed Employers information requirements (EIR) for a flawless exchange
The agreed Employers information requirementswere also an important part of the project and were drawn up in great detail. These documents clearly set out the information requirements specified by the client. Therefore, it was clear to everyone involved which information had to be provided by the respective contractors at a certain time and in a certain quality. For this construction project in particular, which is to be handed over to facility management at a later date, it was important that the required information was stored in the model. For the TÜV SÜD project, this included the following information in particular:
- Project information (project name, description, location)
- List of project participants with contact details, roles, competencies and responsibilities
- Summary of the BIM project objectives and the strategies for achieving them
- Description of the information requirements
- Description of the information models to be used (reference model, specialist models, coordination models, process models, cost models, simulation models, etc.)
- Modeling and attribution guidelines for the digital description of areas, rooms and objects
- Description of the rules for labeling and classifying areas, rooms, objects and documents (location, facility, inventory, document labeling, etc.)
- Description of the IT infrastructure and software landscape including collaboration platform, document management systems, databases, BIM model server, BIM software of the specialist designers, digital room, facility and inventory books, tendering software
- Description of the strategies for the exchange of information between the project participants (with regard to interfaces, exchange formats and schedules; milestones)
- Project progression regarding Level of Detail (LOD) and Level of Information (LOI)
- Description of quality management & workflows for quality assurance
Interoperability as the key to success
Thanks to the use of LINEAR software, PLANplus was able to seamlessly implement all the requirements for the HVAC and MEP systems. The pronounced interoperability and the open interface for data exchange played a decisive role in this. This ensured that a wide variety of systems and devices could communicate smoothly with each other, allowing all users to work together seamlessly without generating additional work. The software gave everyone involved in the project access to the same data and enabled this information to be updated in real time. The automatic collision check helped to identify conflicts between trades at an early stage. External, cloud-based programs were also used for coordination.
Laser scan as an additional service
In addition to BIM design, PLANplus also offers laser scanning for existing building strucutres. In this project, this also enabled precise digital documentation of the building and the installation areas before the walls and ceilings were sealed, which is particularly important for the subsequent usage and facility management. Thanks to the digital representation, it is possible to “inspect” the model at any time using VR technology or a PC in order to optimally plan and carry out maintenance or expansion tasks.
At the end of the desing services, a digital twin is therefore available for handover to the facility management of the building operator TÜV SÜD.
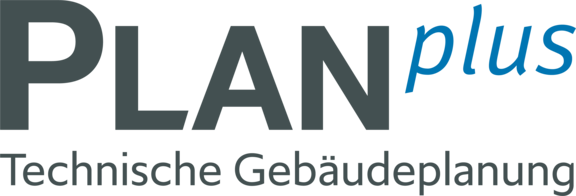
PLANplus Technische Gebäudeplanung is an independent engineering office for BIM design of technical building equipment in industrial, commercial and residential construction.
The office was founded in 1997 by Rudolf Steger. With a team of currently 20 employees, consisting of engineers, technicians and system designers, PLANplus works with the most innovative digital design methods.
The BIM design method was introduced throughout in 2015. Since 2022, the complete BIM design service has been offered for all technical trades (HVAC/MEP/MSR/SPR/electrical). In the industrial and commercial sector, the company uses Scan2BIM to create digital twins.
Since 2021, PLANplus has also been working with its strategic partner Sustainable Exergy in the field of sustainable energy generation and low-loss control of energy flows for maximum independence and cost-effectiveness.
The author
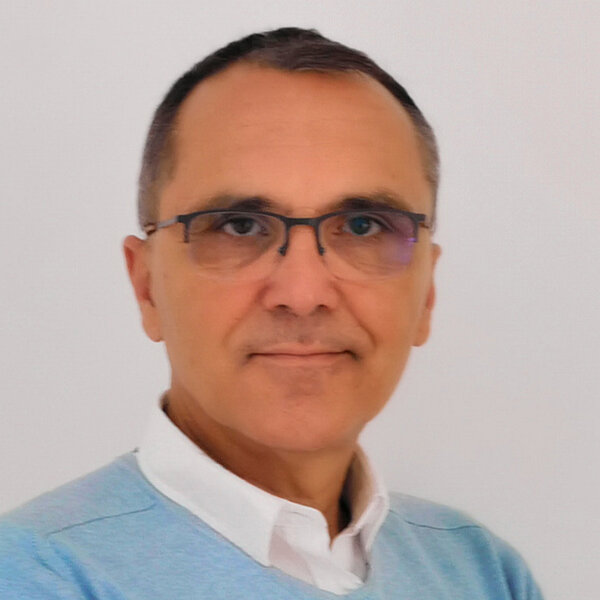
Rudolf Steger
Founder and
Branch Manager
Kirchheim near Munich