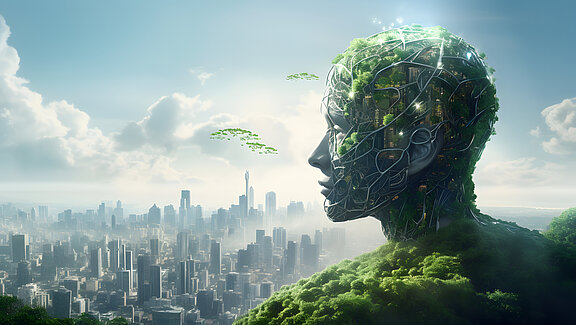
Image: © Clipart Collectors – stock.adobe.com
The life cycle assessment method provides a basis for sustainable planning and evaluation of the environmental impact of a building in order to assess these influencing factors and the building's energy consumption during operation. This paper presents the basics of life cycle assessment at a national level and provides information on how technical trades in particular can influence the life cycle assessment of a building (see Fig. 1).
What is the scope of a building's life cycle assessment and which terms are relevant?
Life cycle assessment (LCA) is a tool for calculating the environmental impact of a building over a defined period of time. The energy consumption of a building and the resulting emissions are caused on the one hand by all the building materials used in the building and on the other hand by the energy required for heating, ventilation, cooling and lighting during the use of the building. Figure 2 shows the cycle of materials and thus the scope of a building in a life cycle assessment.
In order to conserve finite material resources and achieve a small CO2 footprint (eco-balance) for the building, particular attention must be paid to ensuring that the materials and components used can be easily dismantled at the end of the building's useful life and that they are unmixed and low in pollutants. This ensures that they can be reintroduced into the material cycle and reused if possible without devaluation (reuse) or with minimal devaluation (recycling) and with as little waste as possible. Materials that cannot be recycled leave the cycle at this point and end up in landfill or thermal recycling due to a lack of technical know-how and economic viability.
The life cycle phases of a building that are taken into account in a life cycle assessment are regulated in the DIN EN 15978. According to an extract from this standard, the production phase (A1 - A3), construction phase (A4 - A5), operational phase (B1 - B7), disposal phase (C1 - C4) and the potential for reuse, recovery and recycling (D) are taken into account in the life cycle assessment (see Fig. 3).
Which environmental indicators are evaluated and where does the data come from?
The life cycle assessment evaluates the environmental impact of a building in terms of emissions. The evaluation distinguishes between the global environmental impacts and the global use of finite resources (see Tables 1 and 2). The overview tables briefly explain the environmental indicators usually evaluated in a life cycle assessment and how they are influenced.
Ideally, the key data required for the assessment is provided by the manufacturers of the construction products in environmental product declarations (EPDs). The EPDs based on the EN 15804 provide comparable information on the environmental performance of products, which are output in accordance with at least the environmental indicators defined in Tables 1 and 2 and the phases shown in Figure 3 (see example extract from the Environmental Product Declaration of a volume flow controller from Wildeboer Bauteile GmbH in figure 7).
In addition to the product specific EPDs, generic data sets of EPDs for individual building materials (e.g. concrete, copper) are also commissioned and published once a year by the BBSR (Federal Institute for Research on Building, Urban Affairs and Spatial Development of Germany). These are provided on the basis of generally accessible statistics and data. For the life cycle assessment of buildings, generic data sets are currently still used for most materials. One reason for this is that the database of available EPDs is still being compiled using manufacturer information.
The basis for calculating the life cycle assessment is DIN EN 15978. The components used are classified according to DIN 276 and their respective quantities and masses are recorded according to cost groups 300, 400 and 500 (for outdoor facilities involved). Depending on the reference unit (m, m², m³, number etc.) of the EPD used, a conversion to the correct reference value is necessary. In the case of digital images of components to be included in the balance, a specification of the reference value (static product models) or a geometric or rule-based measurability (parametric modeling) is therefore a mandatory prerequisite for a model-based calculation.
Is there currently a legal obligation to prepare a life cycle assessment for a building?
Currently, there is (still) no legal obligation at national level in Germany to prepare a life cycle assessment of a building. In the future, there are plans at European and national level to document the life cycle assessment by issuing a resource passport for buildings. However, life cycle assessments are already required today as part of sustainable building certifications, e.g. according to DGNB (German Sustainable Building Council), BNB (Assessment System for Sustainable Building) and as part of the Federal Funding for Efficient Buildings (BEG). These are discussed in more detail below.
For buildings with funding under the BEG (Federal Funding for Efficient Buildings), the life cycle assessment and compliance with limit values have become a component of the funding for new buildings. Since 03/01/2023, the funding program has been referred to in the BEG as Climate-Friendly New Construction (KFN). The life cycle assessment must be verified in accordance with the so-called QNG boundary conditions - a quality seal for sustainable buildings. The QNG requirements are limited to the permissible greenhouse gas emissions and the permissible non-renewable primary energy demand in the building life cycle. For a residential building, for example, the limit value for QNG-Plus is a maximum of 24 kg CO2 equivalent/m²a for greenhouse gas emissions and a maximum of 96 kWh/m²a for permissible non-renewable primary energy demand. For non-residential buildings, the requirement values are determined individually on the basis of the energy balance of the building. The special calculation specifications according to QNG are to be followed here. Module D (recycling potential and effects of exported energy), for example, is not included in the balancing, but only shown separately (for information purposes).
Different boundary conditions, different limit values and different evaluation rules apply both for the different sustainable certification systems and for subsidies under the BEG. For example, defined EPD datasets must be used for the QNG, while the current generic datasets of ÖKOBAUDAT (national database for the life cycle assessment of buildings) must be used for the life cycle assessment, e.g. according to DGNB. As a result, two life cycle assessments must be prepared for buildings with certification and subsidies according to the BEG, one according to DGNB boundary conditions and the other according to QNG boundary conditions.
Influence of MEP on Life Cycle Assessment
The greatest potential for positively influencing the eco-balance of a building is to dispense with materials or reduce the amount of materials used to a minimum. Another necessary objective is the implementation of climate-neutral building operation. The MEP disciplines have a major influence on the life cycle assessment through the selected energy supply concept, but also through the number and selection of materials in the MEP construction and the refrigerants used.
Production Phase A1 - A3
In the production phase, the materials are assessed in terms of their global environmental impact for the procurement of raw materials, transportation to the plant and production of the material. The system boundary covers the processes "from the cradle to leaving the factory premises". In line with the system boundaries of life cycle assessments as part of certification processes, only the building materials and materials in cost groups 300 (building structures) and 400 (technical equipment) are recorded for construction.
The supporting structure (cost group 300) represents the largest share of the global environmental impact in terms of global warming potential and primary energy demand. In addition to this, in MEP design, the selection of materials with a low environmental impact, reusable and recyclable building materials and components and as little bonding as possible can have a positive influence on the life cycle assessment.
Comparison of the global warming potential with regard to the choice of materials
Figure 4 uses generic data sets from ÖKOBAUDAT from 2022 to compare five potable water pipes made of different materials in terms of their global warming potential. A stainless-steel potable water pipe is compared with four different plastic potable water pipes. The illustrated evaluation refers to potable water pipes with a nominal diameter of DN 12 per meter of pipe length. In terms of mass, stainless steel has a lower CO₂ equivalent than plastic. Due to the higher weight of stainless steel potable water pipes per meter, plastic pipes have a lower global warming potential. This diagram is not intended to give the impression that the use of plastic pipes is fundamentally more sustainable than stainless steel pipes. After all, recyclability and dismantling friendliness as well as the reuse of materials and the closing of material cycles are playing an increasingly important role in the construction process.
For example, stainless-steel products do not require waste treatment, as stainless steel is largely made from alloyed scrap metal, thus minimizing the use of limited resources. Furthermore, almost 100% of stainless-steel products are nowadays recycled, while most plastic waste is currently sent to energetic utilization.
When selecting materials, it is therefore not only the production process that plays a decisive role, but also the recyclability and reusability of the individual materials. The priority when saving resources should therefore be avoidance - do we even need this material? In the second step, the focus is always on "preserving" the material in its original form and reusing it in the construction process. For a stainless-steel pipe, for example, this means that it can be removed at the end of a building's life and reused (without being melted down) in another building (reuse) if hygiene requirements are met at the same time.
Preparation of life cycle assessment on the example of funding requirements for climate-friendly new construction (BEG QNG)
According to QNG boundary conditions, components and component constructions of cost group 400 are recorded collectively with the so-called base amount, e.g. pipes and manifolds for heating surfaces of cost group 420. This applies to the production phase A1-A3, the replacement B4 and the disposal phase C3 and C4. Data records for large systems technology, such as heat generation systems, ventilation systems, self-supply systems and elevator systems, must be added to the base amount in accordance with the QNG data records and specified replacement cycles. The following table shows the base amounts for greenhouse gas emissions and non-renewable primary energy demand for the QNG-Plus and QNG-Premium requirement levels.
Even if there is a base amount for cost group 400 in the context of life cycle assessments in accordance with QNG, the actual quantities and masses must be taken into account for life cycle assessments with other boundary conditions (e.g. for certification procedures). The increased efforts of manufacturers to create EPDs for their technical components indicate that the choice of resource-saving technical components will become more important in the future.
Operational phase B1 - B7
The life cycle assessment of a building is usually considered over a period of 50 years. The requirements to be applied are based on the final energy requirements from the building physics certificates in accordance with the German Building Energy Act (GEG). Experience has shown that the operational phase accounts for more than 50 % of the greenhouse gas emissions of a building life cycle. As an example, Figures 5 and 6 show the results of a life cycle assessment according to QNG boundary conditions for a school building as a solid construction and with an air-to-water heat pump.
The more renewable energies and systems for self-generated electricity are included in the building design, the better the life cycle assessment and the lower the environmental impact of the building in terms of emissions during the use phase. The selected energy concept can have a significant impact on the ecological footprint of a building throughout its entire life cycle. Furthermore, the global environmental impact of a building can be further reduced through low-tech concepts (e.g. night ventilation via ventilation flaps in window facades). By dispensing with or deliberately reducing technical components and selecting robust, durable building technology, no or fewer technical components need to be replaced during the life cycle of a building. As the MEP components are only considered to have a service life of 10 to 25 years in the life cycle of a building, robust system technology with longer life cycles should be selected. This not only saves money (investment, reinvestment and maintenance), but also resources.
Influencing a life cycle assessment example of refrigerant selection
The choice of refrigerant can have a positive influence on the life cycle assessment. For example, according to the QNG boundary conditions, only natural refrigerants in accordance with AMEV Kälte 2017 (Guidelines for planning, construction and operation of refrigeration systems and cooling units for public buildings of the Working group for mechanical and electrical engineering in national and local administrations) table 4 (e.g. R290 - propane and R717 - ammonia) and refrigerants classified as future-proof until 2030 in accordance with AMEV Kälte table 3 (e.g. R1234ze and R454A) should be used. This requirement applies to HVAC systems as well as refrigeration systems and heat pumps. This requirement is intended to avoid the additional global environmental impact of non-natural refrigerants. The GWP factor of non-sustainable refrigerants is, for example, 2088 kg CO2-equivalent per kg refrigerant for the refrigerant R410A, whereas the GWP factor for a sustainable refrigerant for e.g. R290 is 4 kg CO2-equivalent per kg refrigerant. This means that in this case, the non-sustainable refrigerant is 522 times more harmful to the climate than the sustainable refrigerant.
The GWP factors of the refrigerants are not usually included in the life cycle assessment, as the avoidance of additional global environmental impacts caused by refrigerants is already ensured by the above-mentioned requirements. For buildings with refrigerants that do not comply with the mentioned boundary conditions, the effects of refrigerants on the global environment must be recorded in the relevant period for Module B1 and assessed as global warming potential. The calculation results are added to the LCA results. Leakage rates, disposal rates and replacement cycles must also be taken into account in accordance with the QNG boundary conditions. This procedure ensures that the global environmental impact of non-natural refrigerants is taken into account in the LCA according to QNG. By choosing the "right" (sustainable) refrigerant, the LCA and the global environmental impact can be greatly influenced in the MEP design process.
Conclusion
MEP design has a major influence on the global environmental impact of a building. The possible influences presented in this paper result from the selected MEP materials in the production phase of a building, the selected energy concept with consideration of the necessary number and robustness of the MEP components in the operational phase, the recyclability of the materials in the material cycle and the selection of environmentally friendly refrigerants.
How sustainable a building will be later is not decided in stage 3 (design) with the verification of the building design. Sustainable planning begins in early deign stages (stage 0) with the definition and initial validation of the objectives for the use of the building. It requires an interdisciplinary planning approach by all specialist planners from the beginning of stage 2 (preliminary design).
Only then can any future task of all those involved in the planning process be realized. This includes the reduction of global environmental impacts, the consideration of the recycling of building materials at the same level after the end of a building's life cycle and the avoidance of construction waste. Resource-conserving construction and thus the reduction of global environmental impacts are among the most important goals and challenges facing the construction industry in the coming years.
Authors
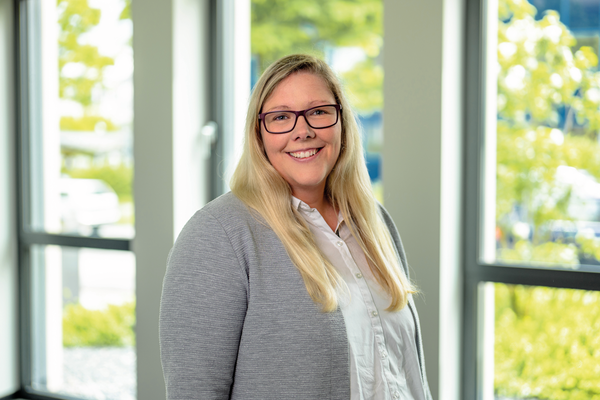
Carina Hollenbeck
Authorized Expert for Sustainable Building
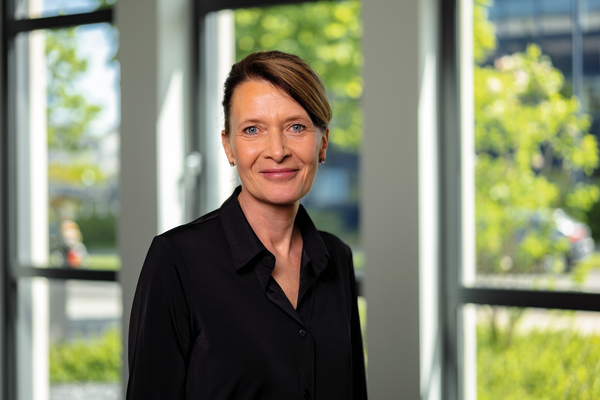
Ines Naumann
Head of Competence Center Sustainable Building
With more than 340 employees, KEMPEN KRAUSE INGENIEURE provides planning, control and monitoring services for demanding construction projects in almost all specialist disciplines of civil engineering. Resource-conserving planning has always been part of our planning DNA. That's why our engineers are ideally equipped for the latest developments - sustainability, timber and timber hybrid construction, recyclable building materials, cradle-to-cradle and low-tech projects. Naturally, with the latest BIM-based planning tools. This is why our planners, particularly in structural design, fire protection and building physics carry out many projects using end-to-end 3D models (Building Information Modeling - BIM), thereby optimizing planning, construction management and the use of buildings, both in structural and civil engineering. Mobile 3D scanners and drones for building detection, intelligent planning tools, targeted knowledge management and a lifelong willingness to undergo further training characterize our self-image as a service provider.
KEMPEN KRAUSE INGENIEURE GMBH
Ritterstraße 20
52072 Aachen
0241/88 990 0
www.kempenkrause.de
info@kempenkrause.de